The satellite industry is experiencing tremendous growth of space-based systems ranging from the large, billion dollar projects such as the James Webb Space Telescope to smallsats used by the private and academic sectors for smaller commercial and research projects.
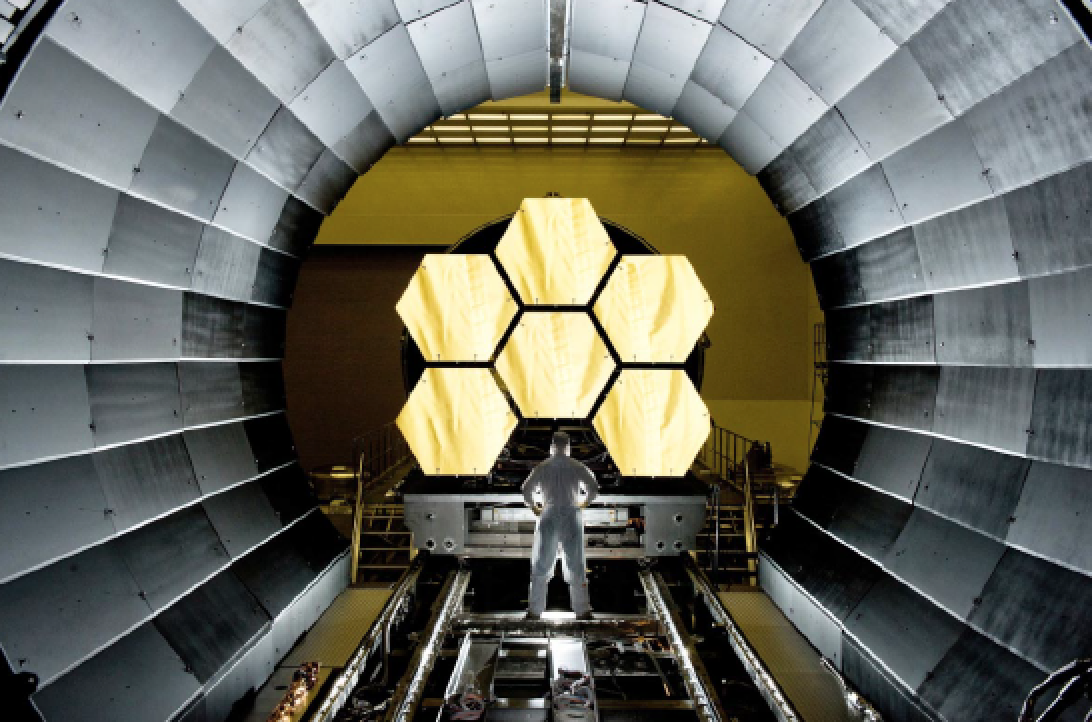
Materion’s O-30-H beryllium was originally developed to make the mirrors for the James Webb Space Telescope (JWST) Photo is courtesy of NASA.
All these data-gathering programs are designed to understand and predict events impacting the planet or ensure commercial success through weather forecasting, monitoring climate change, predicting crop yields and the utilization of mineral resources.
Other missions such as those for Global Positioning System (GPS) navigation, global communications, scientific exploration and national defense also contribute to the expansion of space-based systems.
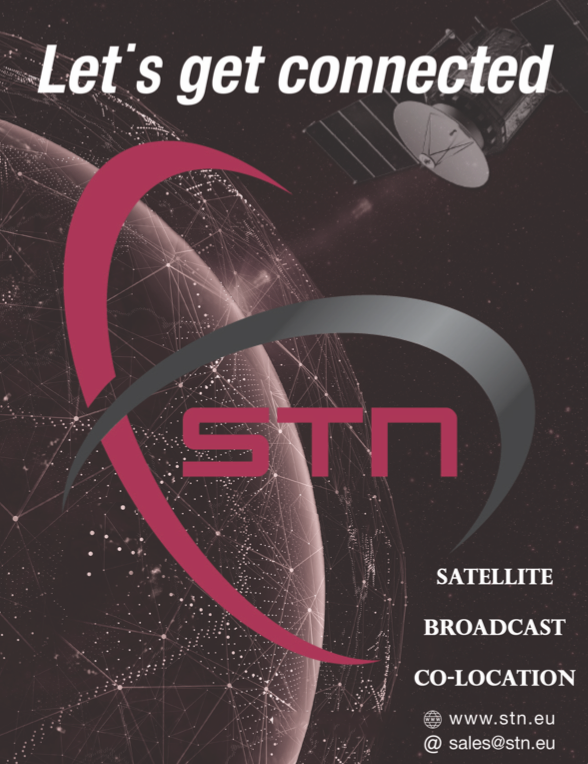
While the applications vary — from reflective optical systems, structural components, mechanisms and thermal management solutions — the unique demands of the operating environment require the use of materials that perform reliably in extreme temperature ranges.
Design teams must look beyond conventional materials, utilizing advanced materials to enhance and enable sophisticated space technologies. As space technologies advance, new materials that exhibit great potential for the next generation of space programs are needed.
Advanced Materials for Space-Based Systems
Materion offers advanced materials that provide a range of benefits for space applications, including beryllium metal, aluminum beryllium, investment cast aluminum beryllium, and aluminum silicon carbide metal matrix composites (MMCs).
Beryllium Metal Because of its high performance and reliability, beryllium has been used consistently on space structures since the inception of space programs. It has the highest specific stiffness of any metal with a modulus of 44 msi and a density of 0.067 lb/in3 — six and a half times that of other metals. This differentiating property means beryllium is better equipped to maintain its properties even with the harsh environment changes in space. Beryllium is available in a range of grades and product forms. One that has proven successful in many space programs is produced through powder metallurgy and is consolidated through a Hot Isostatic Pressing (HIP) process. It provides adequate strength, with an ultimate tensile strength (UTS) of 60 ksi and a yield strength of 43 ksi. Beryllium’s strength properties, combined with its coefficient of thermal expansion (CTE) of 11.3 ppm/0C and its isotropic expansion allow design engineers to create very stable optical systems across a range of operating temperatures. For example, a beam steering device used in a space-based laser communications application, when made from beryllium metal, can position a mirror extremely accurately at very high speeds and do so across a wide range of temperatures while maintaining adequate strength to survive launch loads. Beryllium metal is also used in some thermal management applications because it has good thermal properties. One grade of beryllium has a thermal conductivity of 216 W/m.K and a heat capacity of 1.95 J/g.K. This is important because the beam steering device may include an electronic housing and frames that must conduct heat away from the device and associated electronics. While this is just one scenario, there are many other specific space-based applications where beryllium provides critical thermal benefits. Beryllium’s properties have led to its successful use for more than 50 years in space applications. This success can be attributed to beryllium’s exceptional properties and performance, but not all of today’s space-based systems require the same level of high performance. As commercial satellites become more common, other advanced materials can offer the appropriate property sets better suited to those applications and their unique needs. Metal matrix composites are one type of material that supports new satellite technologies by providing a range of properties that align with the needed level of performance.
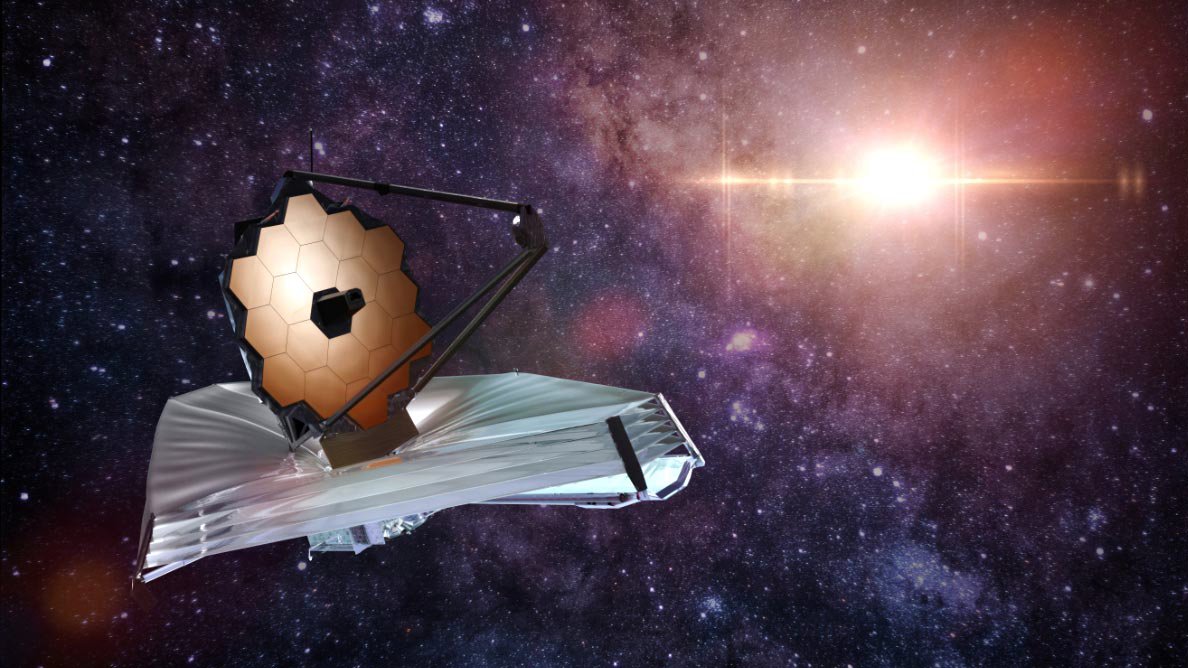
Artistic rendition of the James Webb Telescope
Aluminum Beryllium Metal Matrix Composites Aluminum beryllium MMCs such as Materion’s AlBeMet have the highest specific stiffness for any MMC with a modulus of 28 msi and a density of 0.076 lb/in3 —that means it has a specific stiffness that is more than three and a half times that of traditional aluminum. The most common grade of AlBeMet composite contains 62 percent beryllium and is made through a powder metallurgy method where gas atomized aluminum beryllium powder is consolidated through a HIP process. This grade provides the needed level of performance with significant improvements in manufacturability. To date, AlBeMet composites have been used in more than 150 satellites that are currently flying in space in applications including electronics housings for thermal management and many reflective optical systems. Investment cast aluminum beryllium material such as Materion’s AlBeCast® alloy offer another solution for applications not requiring the extremely high-level performance of beryllium. This material has a similar specific stiffness compared to aluminum beryllium composite HIP product. Using an example of a space-based beam steering device again, it may be advantageous to make the gimbal structures from AlBeCast investment castings and the mirror from AlBeMet composite. This way, the structures offer many performance advantages with less input material and lower fabrication costs.
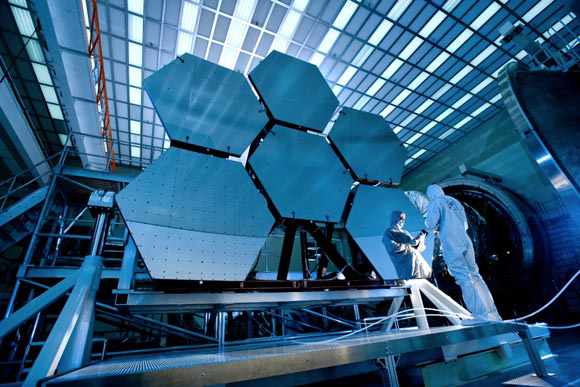
Beryllium’s unique property characteristics make it a critical
material for optical space applications. Photo is courtesy of NASA.
Aluminum Silicon Carbide Metal Matrix Composites Many reflective optical and electronic systems are produced using aluminum alloys such as AA 6061, but sometimes higher system performance is needed than is possible with conventional materials. An ideal solution for this situation is aluminum silicon carbide (AlSiC) MMCs such as Materion’s SupremEX composites. AlSiC MMCs are manufactured through powder metallurgy, which, combined with a proprietary high energy mixing process, produces a HIP material with a highly refined and homogeneous grain structure. This product group provides improved stiffness, high specific strength, elevated temperature strength, fatigue strength and a lower CTE than aluminum. SupremEX 640XA MMC was specifically developed for applications requiring stiffness and stability. This grade is manufactured from a gas atomized AA6061 powder and 3.0 micron SiC powder with a modulus of 20.3 msi and a density of 0.105 lb/in3, resulting in a specific stiffness that is almost double that of aluminum. SupremEX 640XA has a CTE of 13.4 ppm/0C, which is isotropic and is a very close match to AlBeMet AM162H at 13.9 ppm/0C. This allows both materials to be used together in optical system assemblies to produce stable optical performance across a range of working temperatures. Some grades of SupremEX MMCs were also developed to improve manufacturability and provide extruded sections, rolled sheet, foils and forgings, offering greater potential for use in satellite applications.
What’s Next for Advanced Materials
As satellites continue to evolve and more missions emerge, the need for advanced materials will continue to grow. Manufacturing technologies such as investment casting and additive manufacturing will play a critical role in this evolution and materials providers like Materion will continue to adapt to ensure that material solutions properly support the growth of the space industry.
materion.com
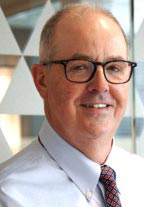
Martyn is the Global Defense Market Director for Materion and has an extensive background in working with beryllium metal, aluminum beryllium and aluminum silicon carbide metal matrix composites. His focus is to provide customers with advanced materials solutions that meet their next generation defense application needs. He has over 40 years’ experience in the manufacturing industry, suppling products for aerospace, defense, space, automotive, and nuclear power generation markets.