Equipment used in space applications needs to go through stringent environmental tests in order to prove that survivability within the extreme conditions experienced during launch or while in space. Some of the key environmental tests include vibration, thermal vacuum and electromagnetic compatibility.
• Vibration test is important to ensure that the equipment is able to sustain high impact during the rocket launch and planetary landing
• Thermal vacuum test is crucial to confirm the equipment is able to operate under space vacuum condition
• Electromagnetic compatibility test is required due to densely packed electronic systems operating in various frequencies. RF signals radiated from high power equipment (transmitters) can affect the performance of low power equipment (receivers)
This article focuses on the thermal vacuum (TVAC) test, which is typically the final as well as the most complex and expensive test to be conducted. Detailed planning is typically required six to 18 months in advance in order to ensure the success of the test.
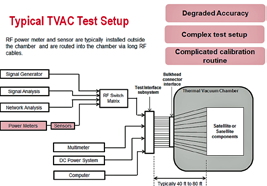
Figure 1. Typical TVAC test setup with all the measurement equipment located outside of the chamber and connected to the satellite or components via switch matrices or test interface subsystem.
TVAC testing helps to uncover possible problems, such as outgassing of equipment that could contaminate the environment, design flaws due to short circuits or overheating of materials, and corona (metal vapor arcing) effect. In this article, the existing power measurement test setup for TVAC test and a new method with a TVAC qualified LAN power sensor will
be compared. The new proposed method provides a simplified test setup and more accurate, reliable power measurements for TVAC testing of satellite equipment.
Typical TVAC Test Setup
Figure 1 below shows the typical test setup for a TVAC test. The whole satellite or satellite components/modules are placed inside a TVAC chamber. All electrical connections to the system under test must include hermetically-sealed connector feedthroughs in order to maintain the vacuum. In general, all the measurement equipment, including power meter and sensors, are located outside of the chamber and are connected to the satellite or components using the sealed feedthroughs via switch matrices or a test interface subsystem.
Long RF cable runs are often needed to connect the power sensor to the satellite inside the chamber. This results in degradation in accuracy due to poor SWR and insertion loss from the long RF cable. Complex calibrations are required to calibrate the path loss as the RF cable performance changes with temperature.
New TVAC Test Setup
With a TVAC qualified power sensor, the sensor can now be connected directly to the satellite inside the TVAC chamber (see Figure 2 below). The benefits include:
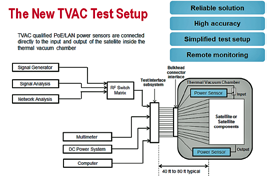
Figure 2: New TVAC test setup with sensors connected directly to the input or output of the satellite for improved accuracy and a simplified test setup.
• Simplifying the test setup and complex calibration routine. You can now connect the sensor directly to the output of the device-under-test, removing the need to go through a long RF cable that requires complex calibrations in order to calibrate out the performance changes of the RF cable due to temperature effects. The power sensor will provide accurate output power measurements immediately without path loss calibration
• More reliable and accurate power measurements. Eliminating the long RF cable removes power measurement uncertainties due to insertion loss, poor SWR performance and temperature effects of the cable. The power sensor is fully calibrated and offers warranted accuracy specifications over a wide temperature range of 0 to +55˚C. The sensor’s internal zero and calibration function also allows users to perform zeroing and calibration on-the-fly to improve overall measurement accuracy
• Remote monitoring. By connecting the LAN power sensor to a shared network via network switch or Power–over-Ethernet (PoE) hub, the power sensor can be controlled remotely from any part of the world.
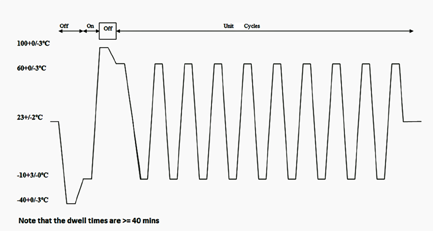
Figure 3. Keysight TVAC qualification test profile for U2049XA, Option TVA. The test was carried out over duration of 10 days with eight hours per temperature cycle. Performance tests were carried out throughout the different hot and cold temperatures to ensure that the sensor is able to measure accurately over a wide range of temperatures under vacuum environment, and that repeated temperature cycling does not degrade performance.
The benefits of using the TVAC power sensor compared to a traditional bench power meter and sensor solution are shown at the top of the next column..
Design + Qualification Process Of TVAC Power Sensor
Several steps are required to develop a TVAC power sensor.
1. Selection of low level materials
TVAC power sensors are built with low level materials with minimum outgassing properties. All the materials used should be matched against the NASA/ESA outgassing database and items not listed in the database should be subjected to a screening test in accordance with ECSS-Q-ST-70 02C 02C (Thermal vacuum outgassing test for the screening of space materials by European Cooperation For Space Standardization) to ensure any outgassing is within prescribed limits.
2. TVAC qualification test
After the entire sensor has been developed with materials that meet the low outgassing criteria, the full sensor assembly needs to go through a TVAC qualification test whereby the sensor is subjected to operation tests ranging from -10 to +60 ˚C and non-operating storage tests from -40 to +100 ˚C inside a thermal vacuum chamber. Power measurement readings in a low pressure environment inside the TVAC chamber will be compared to measurement readings at atmospheric conditions to ensure that there are minimum variations in accuracy between these different environments.
3. TVAC bake out
Finally, as part of standard production test processes, every TVAC power sensor will be subjected to thermal vacuum bake out in a TVAC chamber at high temperatures for several hours. The purpose is to remove all possible outgassing particles. At the end of the bake out process, the sensor will be immediately packed into a vacuum sealed bag to minimize reabsorption of moisture. With this process, users can be assured that the sensors they receive are contaminants-free and will not contaminate the TVAC chamber during TVAC tests.
A LAN power sensor with a TVAC option is ideal for long distance remote monitoring of satellite or components inside a TVAC chamber. The sensor helps to improve power measurement accuracy and simplify the test setup and calibration process. The new proposed method is able to provide a simplified test setup and more accurate, reliable power measurements for TVAC testing of satellite equipment.
With its patented internal zeroing and calibration capability, wide 90 dB dynamic range and frequency range of 10 MHz to 33 GHz, the Keysight U2049XA wide dynamic range LAN power sensor is ideal for satellite applications. The thermal vacuum option (U2049XA-TVA) is ideal for usage inside a thermal vacuum chamber.
For more information, please refer to the application note at keysight.com/find/rfpowertips