Along a neatly landscaped road in Mountain View, California, sits an understated industrial building. The building houses a newly installed Moog electrodynamic shaker table.
Moog engineers anchor satellite parts atop the table to detect the minutest failure stemming from vibration. Customers are paying Moog to do this work to be certain satellite components can withstand the vibration a rocket creates while pushing a payload into orbit. Test specimens range from light-gauge pyrotechnic systems for initiating self-destruct commands to reaction wheels for attitude control.
To trim the cost of vibration tests, experts say some test firms tap technicians who have carried out shock tests or structural analysis, instead of engineers with a deeper technical background. According to the experts, a few years ago, one company in the business of shock-testing satellite components learned it had been acquiring data without anti-aliasing filters in its data acquisition system. An alias signal is a false image or low frequency error indistinguishable from valid data. Aliased signals led to the de-qualification of more than one launch vehicle, as the test firm’s technicians had overstated the qualification loads of many tests.
“Aliasing of digital data is rampant in shock and pyroshock testing,” said Vesta Bateman, a contributing editor to Sound & Vibration magazine.
According to Bateman, “Data acquisition system makers are building and selling systems that allow aliasing. The aliasing phenomena may artificially increase, or decrease, the measured shock level,“ Bateman added.
“Although this problem was identified and addressed in the 1980s, there is a severe loss of this knowledge in U.S. commercial labs,” said Bateman. “Not only is corrupted, aliased data widespread, but it is part of the qualification of equipment operated by people.”
Bateman advocates for higher standards vis-à-vis pyrotechnic shock. However, vibration tests are also vulnerable to anti-aliasing errors. As part of her work, she’s been revising MIL-STD-810G—the world standard for environmental testing (e.g., vibration, shock, pyroshock, ballistic shock, etc.)—to ensure people correctly measure shock to prevent mission failure. Working with experts on the three shock methods in MIL-STD-810, Bateman has offered requirements that prevent aliasing and allow use of a wide variety of data acquisition systems.
An Engineer’s Eye View Of Testing
“Engineers perform our vibration tests,” said Bradley Allen, Test Department Head at Moog in Mountain View. “If we detect a problem with a component, we have the background to solve it.”
Moog runs its vibration tests on an electrodynamic shaker table capable of single-axis control in each of three directions. The table weighs approximately five tons and has a footprint measuring roughly 5’ x 7’, neglecting power and cooling units.
The engineers rely on the table to replicate controlled wave forms such as shaped random spectra, sine and arbitrary inputs, as well as low-level shocks up to 2kHz. Moog performs pyrotechnic shock simulation to 10,000Hz in a separate facility immediately situated next to the vibration test system.
Moog’s tests focus on simulating the environments experienced during launch and in space to verify the integrity of components. A typical vibration test specimen could be a satellite component that Moog has already tested for shock. The customer, such as Aerojet Rocketdyne or Lockheed Martin, wants the satellite’s precision components to undergo vibration testing and often other environmental loads as well.
Moog has performed contract testing for shock and vibration since the early 1980s. Moog says its engineers also design vibration isolation systems, tuned-mass dampers and absorbers, active attenuation systems and other forms of vibration dampers. According to Moog, clean dampers for space and launch applications are one of its core technologies. The company says it can also design damping using a wide variety of technologies.
The bulk of the testing on the new shaker table is for vibration. This is because the shaker table cannot move at cyclic rates high enough to replicate the extremely high-rate oscillatory speeds caused by, for example, pyrotechnics on a launch vehicle.
However, Moog does employ its table for vibration testing of small pyrotechnic systems that carry several grains of charge, often weighing about 1.5kg total. It’s critical to know if the pyrotechnic initiators will survive a rocket launch so they can function on the mission, if needed. Moog engineers can also use the new shaker table to qualify, for instance, a valve the satellite would use to deliver propellant to its thrusters.
The vibration testing Moog undertakes is typically completed in four to eight hours depending on scope. In some cases, the tests require only one engineer to complete them. Once Moog completes a vibration test, the engineers create a test report that includes:
– A description of the test article
– Pictures of the test assembly
– A list of recorded sensors, locations and directions
– Plots of levels imposed on the test hardware, and
– Data file exports of levels measured during the test
According to Moog, one of its most unusual vibration tests so far has been measuring how much cyclic force a reaction wheel generates. A customer wanted to ensure that it could limit the amount of excitation the wheel generates in orbit. The engineers set up an ultra-quiet test table for the job, a table quite different than the newly installed shaker table.
“Some of these forces in orbit can be a fraction of a Newton,” said Allen. “It’s bad if the satellite wiggles, so we identify how much force the reaction wheel reacts back into the satellite and determine whether the test specimen passes or fails the test.”
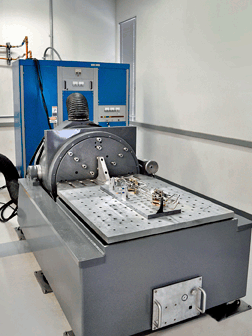
The new Moog electrodynamic shaker table in the company’s Mountain View, California, location with a vibration-isolated Moog latch value affixed for testing. Photo courtesy of Moog.
According to Allen, on one form of test, a customer will give Moog a time domain waveform of acceleration. The controller will send a wave form of voltage that regenerates the acceleration history on the new shaker table. Engineers will also focus on how much vibration occurs as a spectrum of frequency. The test engineer commands and controls the vibration levels for a set period of time. The component receives a failing grade if it no longer works after the test. For example, propellant valves that fail a vibration test will commonly leak afterwards.
Allen said it takes education to understand industry practices and measurement methods, and, often, that’s something an engineer is better equipped to tackle with regard to vibration testing, especially with critical flight hardware.
“As engineers, we’re used to going back and forth readily between time and frequency domains,” said Allen.
Moog’s goal is for customers to continue to return to have satellite components tested on its newly installed shaker table.
Watch the vibration and shock testing video to learn more about the company’s capabilities: http://www.moog.com/sdg-pr/satnews/vibration-testing/csa/
Moog’s infosite for additional information: http://www.moog.com/sdg-pr/satnews/vibration-testing/space
About the author
Bill Perry has written for the manufacturing, financial services and software industries for 20 years. He lives in upstate New York and may be reached at bperry@march24media.com.
About the company
Moog possesses a strong reputation for engineering and product dependability, which has been further strengthened by recent growth. With an emphasis on product development and a commitment to heritage components, Moog is supporting commercial to human rated missions.
Recent additions to the company include:
– Moog Broad Reach is a leading designer and manufacturer of spaceflight electronics and software for aerospace, scientific, commercial and military missions. Also provided is ground testing, launch and on-orbit operations.
– Moog ISP, formerly AMPAC In-Space Propulsion, is a United States and European developer and manufacturer of liquid propulsion systems, engines and components for satellites and missile defense systems.
– Moog Bradford, formerly Bradford Engineering B.V., is a European developer and manufacturer of satellite equipment that includes satellite attitude and orbit control systems, propulsion and thermal subsystems and components.
– Moog CSA Engineering is a recognized world leader in the field of vibration suppression, providing unparalleled experience in the analysis, design and production of a wide array of leading edge, high precision systems. Delivered are innovative products and engineering services to control motion precisely and develop systems that combine vibration and motion control for aerospace and commercial applications.
– Moog has 16 manufacturing and sales facilities across the United States, Europe and Asia dedicated to our space business. Facilities are equipped with complete test capabilities, class 10,000 clean rooms, electronics manufacturing facilities, integration capabilities, and ground to launch to on-orbit support and test.