Gone are the days of designing a system exclusively around traditional, flat, rigid optical shapes. Advances in optical coatings and coating processes enable optical design engineers to test the limits of coated, curved, and unusual shapes within their applications.
Many new hardware technologies function by using only specific bands of wavelengths. In these cases, carefully engineered thin film coatings can be used to select which wavelengths to transmit, reflect, or absorb. These coatings can be found as key components within optical sensors, LiDAR, communication technologies, and more. Expanding potential substrates to include flexible materials, instead of just the traditional rigid ones, offers advantages for applications in which weight and geometries pose a challenge. Advances in thin film coatings expand the possibilities for current and future applications.
Coating Flexible Substrates
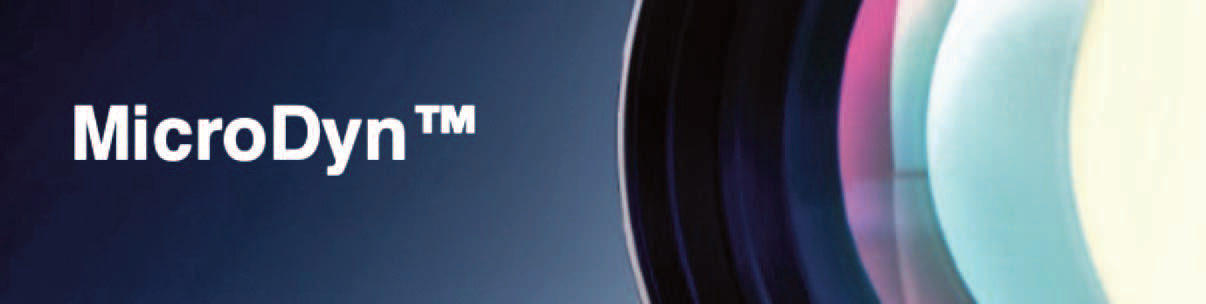
Metals (AI, Cr, Ag, Au)
Semiconductors (Si, Ge)
Oxides (SiO2, Nb2OP5, Y2O3, TiO2, ZrO2, Hf)2)
Nitrides (Si3N4, AIN, TiN)
MicroDyn machines can quickliy produce usable quantities of test material — up to 30 sq. ft. per coating run.
Traditionally, complex thin film coatings have been deposited on rigid substrates such as glass, metal, ceramics and other hard materials, but this list is now being expanded to include flexible substrates such as:
• PET (Mylar, Hostaphan®, Melinex®)
• Polyimide (Kapton®, Upilex®)
• Fluoropolymers (Halar®)
• Polyetherimide (Ultem®)
• Polymethylmethacrylate (PMMA, Plexiglas®, Europlex®) Polycarbonate (Lexan®, Makrofol®)
• Polyethylene
The ability to apply optical coatings to thin, flexible materials means these components can conform to curved or more unusual shapes. A coated thin film can therefore be placed in a wider variety of positions, even potentially around the outside of a device, giving engineers much greater design freedom beyond the traditional form factor of flat, hard optical filtering components.
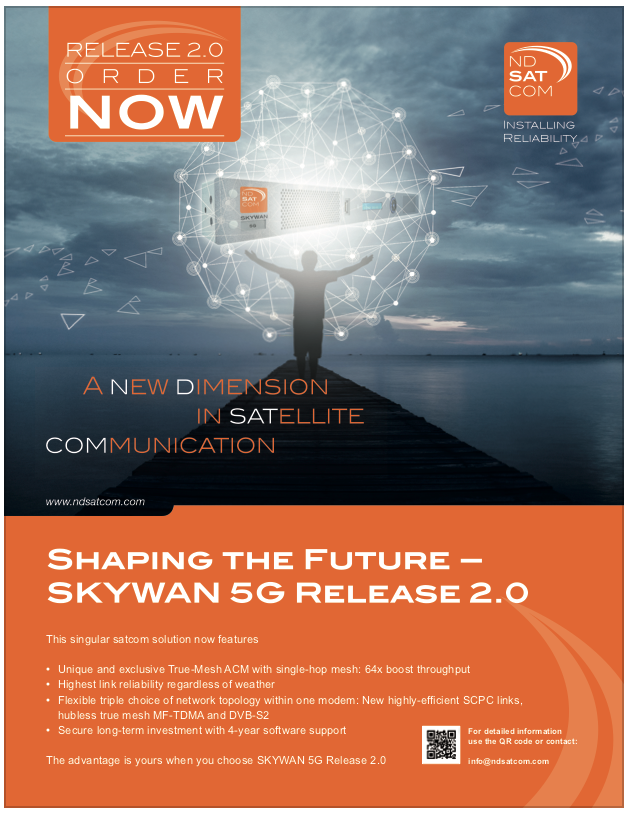
Manufacturing Challenges
The challenge manufacturers face is in the coating process itself. By nature, thin, flexible substrates may not be able to withstand the stressors of the coating application process and handling of the substrate, much less the extreme environmental conditions within their end applications.
Adherence
It’s no simple task to apply and adhere coatings to thin flexible sheets. Plus, with any added strain introduced if the finish product is flexed or twisted, there’s an even higher risk of the coating peeling away from the substrate. To help combat these challenges, coating engineers must come up with innovative methods to help strengthen the bond of the coating to the substrate. One proprietary method uses an intermediate material — a special, additional layer that marries the coating to the substrate. While this method doesn’t yet allow these thin film coatings to withstand repeated, continual flexing, it does increase the product’s robustness so it can be used in environments where there are fewer occurrences of physical disruption.
Testing for Durability Against Environmental Stresses
To ensure performance, it’s vitally important for thin film coatings to be tested in environmental chambers to measure their ability to withstand expected variations in temperature, humidity, and other parameters before they’re incorporated into the final system.
Techniques to Reduce Material Stress During Manufacturing and Handling
Coatings themselves can introduce problematic stresses into the final product. If a coating is applied to a rigid substrate, it’s possible there would be no visible effect from the added stress. However, with a thin, flexible substrate, there is a greater risk that adding a coating could introduce stresses that cause the substrate to roll up onto itself. For example, a poorly designed coating applied to a thin material might cause the part to roll into a cylinder as tight as a pencil. Mechanical instability like this can make the material more prone to tearing or other damage, leading to increased time spent in the installation process.
There are several techniques that can be used to reduce these stresses:
1. Choose the appropriate coating type. The choice of coating type has a large impact on the ultimate net stresses imposed on a component. Where stress is a primary concern, preference is given to coating materials which are inherently low stress. Anti-reflection and electrostatic discharge coatings are two common low-stress coatings. Softer coatings, such as metals, can also be used in applications that have low stress thresholds.
2. Balance stresses on each side of the substrate. Coatings can be carefully engineered with material applied to each side of the substrate, allowing the stress from a coating on one side to cancel out stress from a coating on the other side.
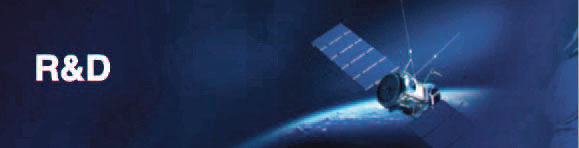
Current Applications
A current example of a high-performance, flexible thin film coating is DSI’s Sunshade material. This material is used to protect communication satellite antennas from the thermal effects of solar radiation while allowing for RF transmission in the S-, C-, X-, Ku-, Ka- and V-bands. This material integrates an electrical charge dissipation function and has low solar absorptance.
The electrical charge dissipation works using an ITO (indium tin oxide) coating. ITO coatings are commonly found in applications such as touch screens. However, in this case, a unique high-resistivity form of ITO was developed to meet the special static discharge and RF transparency requirements of the satellite environment.
Sunshade’s form and ease of handling are as important as the function it brings. Unlike hard, flat materials with thin film coatings applied, Sunshade can be easily rolled, unrolled, and bent to wrap around satellite antennas.
Potential Applications
Solar Cell Technology
New, experimental development methods use precious metal coatings for preliminary steps of solar cell creation. Researchers at the University of Michigan, Ann Arbor, demonstrated in experiments that selectively adding silver or gold within solar cells could boost efficiency by over 8 percent.1
Radiopaque Coatings
In implanted medical devices, radiopaque materials are added so they can be seen during diagnostic imaging.2 Without radiopaque materials, it would otherwise be difficult to detect medical implants and determine whether they are correctly placed in the body when viewing X-ray images. Tantalum is one material currently used for its radiopacity and could potentially be applied and then afterward encapsulated by a medical-grade material.
Devices with Small or Abnormal Form Factors
Electronics embedded within materials with unusual geometries, such as wearable tech and hardware where aesthetics are a primary concern, often use thin-film inner components such as flexible circuit boards. This allows components to easily conform to unusual shapes during assembly.3
While flexible, thin film coatings aren’t currently designed to withstand frequent bending and flexing, it’s possible they could be used in applications where the end form factor is protected by a rigid housing. In these instances, components may only need to be contorted once during assembly and could be candidates for flexible thin film coatings.
www.depsci.com
References
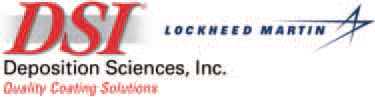
1 Chemical & Engineering News: https://cen.acs.org/articles/92/web/2014/03/Simple-Coating-Gives-Boost-Thin.html
2 wikipedia: https://en.wikipedia.org/wiki/Radiodensity
3 ElectronicDesign: https://www.electronicdesign.com/industrial-automation/designing-ultra-thin-flexible-printed-circuit-boards